Tägliche inbetriebnahme der anlage -7, Tägliche inbetriebnahme der anlage – Hypertherm HD3070 Plasma Arc Cutting System w/ Manual Gas Console Benutzerhandbuch
Seite 76
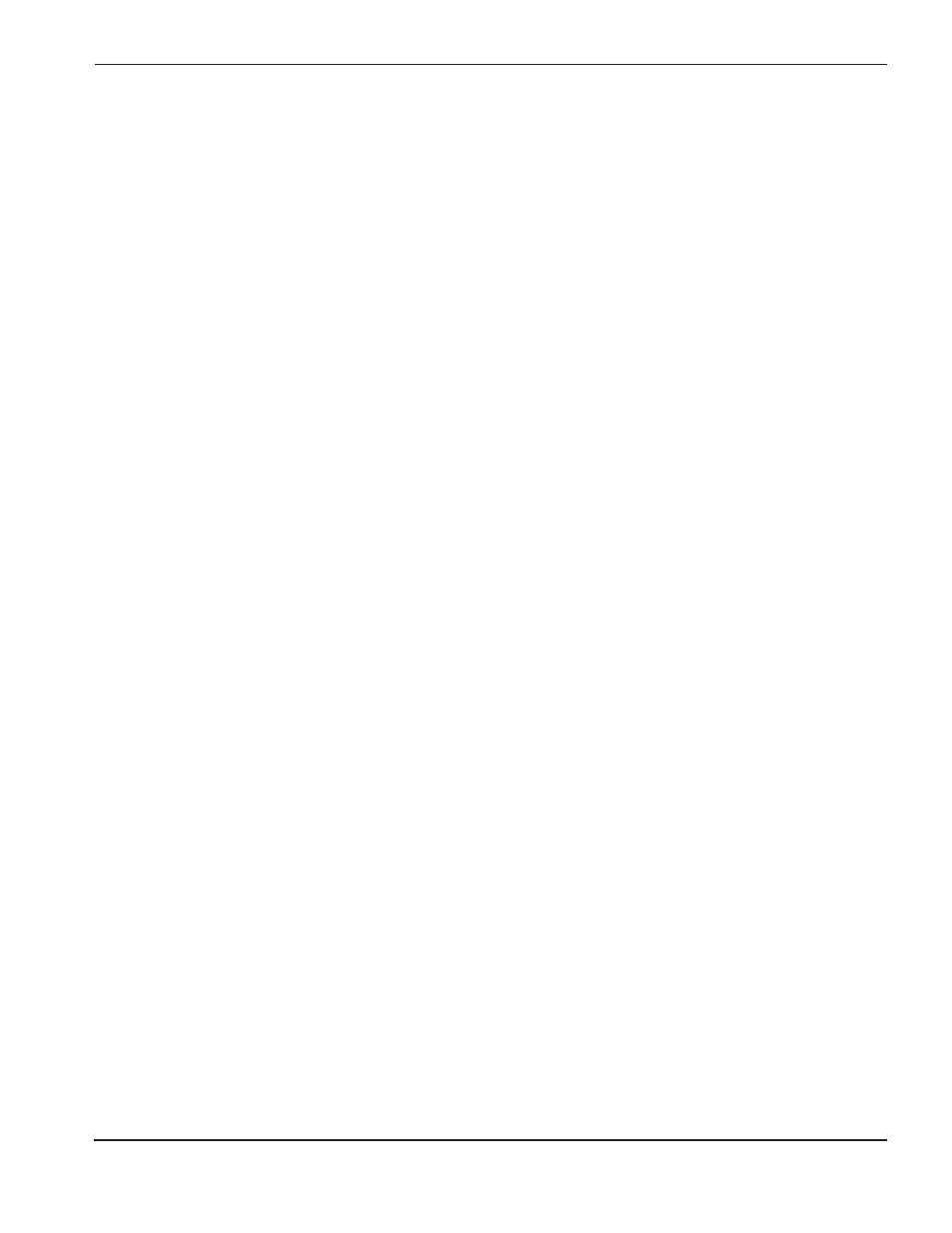
BEDIENUNG
HD3070
mit manueller Gaskonsole Betriebsanleitung
4-7
10/12/98
Tägliche Inbetriebnahme der Anlage
Vor dem Betrieb ist sicherzustellen, daß die Bekleidung sowie die Schneidumgebung den
Sicherheitsanforderungen aus Abschnitt 1, Sicherheit, in diesem Handbuch entsprechen. Sollten während des
Startens der Anlage Probleme auftreten, sind gemäß Abschnitt 3, Installation, die Installationsdaten nachzuprüfen.
Die tägliche Inbetriebnahme enthält die folgenden Schritte zur Einstellung der Anlage für den Schneidbetrieb:
1. Verschleißteile auf Abnutzung und Schäden untersuchen. Siehe Austausch von Verschleißteilen in diesem
Abschnitt.
2. Schneidstrom am AMPS (Ampere)-Kipphebelschalter (S1) auswählen.
Es ist immer der Schneidstrom zu wählen, für welchen die Verschleißteile dimensioniert sind. Es dürfen zum
Beispiel nicht 25 oder 35 A für 30 A-Verschleißteile gewählt werden. Beim Schneiden mit einem Stromwert, der
nicht dem für die Verschleißteile vorgesehenen Schneidstrom entspricht, hat übermäßige Abnutzung der
Verschleißteile und unberechenbare Schneidleistung zur Folge. Es ist außerdem schwieriger, eine
Fehlerbeseitigung bei Schneidfehlern vorzunehmen, da die Basisdaten für andere Werte als 30 A Schneidstrom
nicht vorhanden sind.
3. Es ist sicherzustellen, daß der Brenner rechtwinklig zum Werkstück ausgerichtet ist, damit saubere, vertikale
Schnitte erreicht werden können. Zur Ausrichtung des Brenners ist ein Winkel zu verwenden. Der Brenner sollte
bei 0° und 90° zum Werkstück ausgerichtet werden.
4. Die Anfangs-Brennerhöhe ist gemäß den Tabellen für das Schneiden einzustellen.
Die Ertastung der Anfangs-Brennerhöhe sollte akkurat und gleichmäßig erfolgen, um lange Standzeiten für
Elektrode und Düse zu erreichen. Wenn die Anfangshöhe zu hoch ist, wird der Übergang von Pilotlichtbogen zu
Schneidlichtbogen verhindert oder verzögert. Ist die Anfangshöhe zu niedrig, kann sich beim Lochstechen am
Schutzschild Schlacke bilden und somit die Gefahr eines Doppel-Lichtbogens bei nachfolgenden Starts. Ist das
Schutzschild beim Lochstechen mit dem Werkstück in Kontakt, kann geschmolzene Schlacke zwischen Düse
und Schild gedrückt werden und damit das Sekundärgas nutzlos machen und möglicherweise Schutzschild und
Düse zerstören.
5. Die Einstellung der Lichtbogen-Spannung an der Brennerhöhensteuerung ist gemäß den Tabellen für das
Schneiden vorzunehmen. 1 Lichtbogen-Volt entspricht ca. 0,127 mm.
Die Lichtbogen-Spannung reguliert die Brennerhöhe über dem Werkstück während des Schneidens. Mit einer
höheren Lichtbogen-Spannung wird ein größerer Abstand zwischen Brenner und Werkstück erreicht. Das
Lichtbogen-Spannungspotential liegt zwischen der Elektrodenspitze (tatsächlich am Boden der Einkerbung im
Hafnium-Element) und dem Werkstück. Während sich die Elektrodenspitze abnutzt, bildet sich eine Einkerbung,
und es kann daher notwendig werden, die Lichtbogen-Spannung zu erhöhen, um den größeren Abstand, der
nun zwischen dem Boden der Einkerbung und dem Werkstück entsteht, auszugleichen. So fährt zum Beispiel
der Brenner nach einigen hundert Starts näher an das Werkstück heran und verursacht damit einen negativen
Schnittwinkel. Um diesen negativen Schnittwinkel zu korrigieren, ist die Lichtbogen-Spannung einfach um ein
paar Lichtbogen-Volt zu erhöhen. Der Brennerabstand wird somit erhöht und die Schnittqualität wieder
hergestellt.
6. Das Lochstechverzögerungs-Potentiometer (P1) ist entsprechend den Tabellen für das Schneiden einzustellen.
7. Plasmagas mit dem PROZESS-ANWAHL-Kipphebelschalter (S1) an der rechten Seitentafel der Gaskonsole
auswählen.