Automatik-betrieb – Hypertherm PHC Benutzerhandbuch
Seite 43
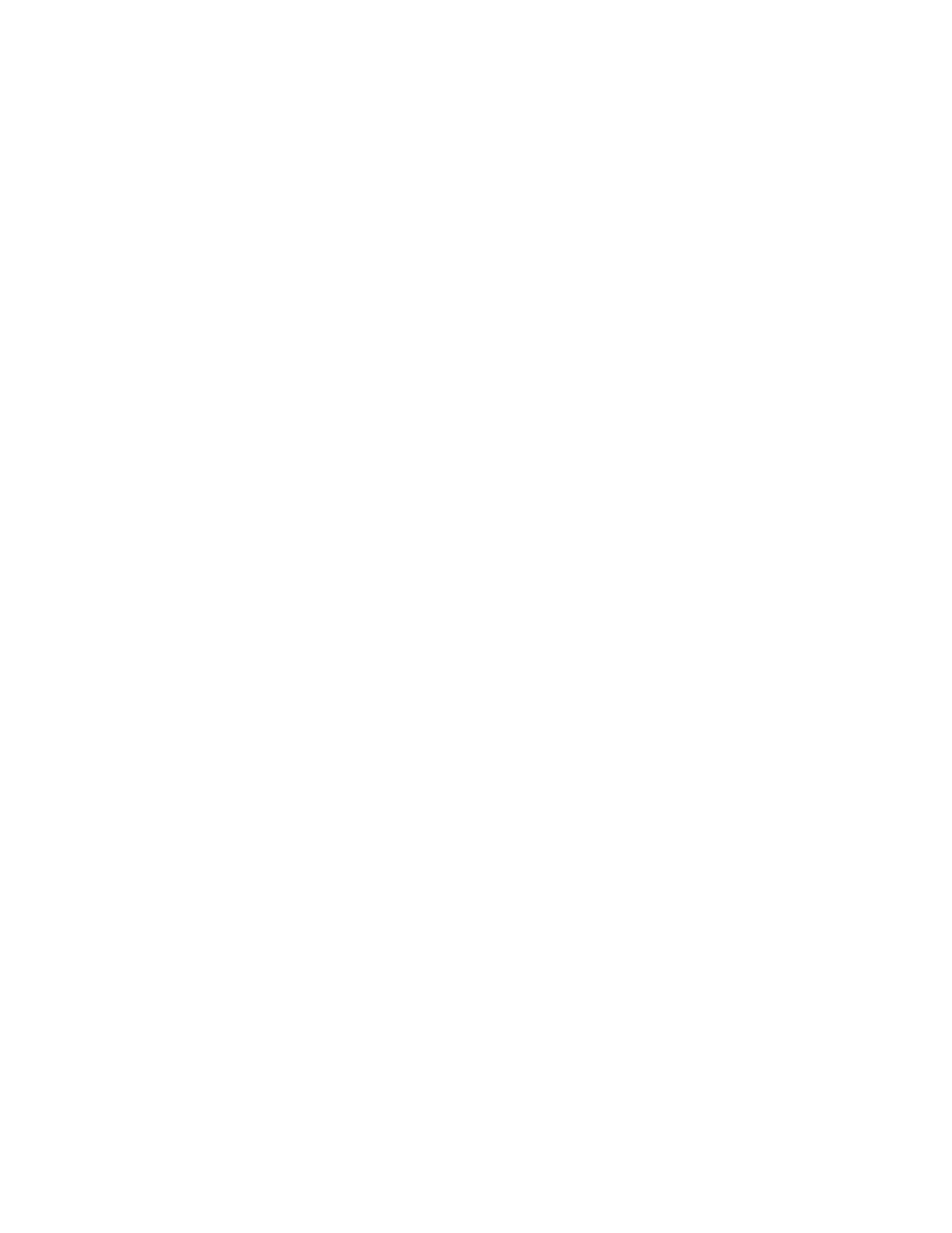
Section 3: Operation
45
Automatik-Betrieb
Der Automatik-Betrieb der Spannungssteuerung wird gewählt, indem der untere mittlere Kippschalter in die
obere Automatik-Stellung gebracht wird. In dieser Betriebsart führt die Einheit automatisch die IHS auf die
eingestellte Lochstechhöhe durch, zündet den Brenner, wartet, bis der Brenner die Platte durchstochen hat
und beginnt mit dem Vorschub des Hubgestells.
Der grundlegende Sensor™-PHC Aufbau für den Automatik-Betrieb besteht aus drei Stufen:
1.
Lichtbogenspannung einstellen.
Verwendung der großen Mehrgang-Regulierung, um die Lichtbogen-Spannung an der Anzeige
einzustellen. Der Anfangspunkt für diese Spannung sollte in den Tabellen für das Schneiden enthalten
sein, die mit der Plasmaanlage mitgeliefert wurden. Es ist wichtig zu bedenken, dass diese Spannung
nur einen Ausgangspunkt darstellt, denn die tatsächliche Lichtbogenspannung hängt von der
Verschleißteilabnutzung, der Länge des Brennerschlauchpakets, den Gasdurchflussmengen und dem
Maschinenvorschub ab. Für optimale Schnittqualität müssen kleine Anpassungen gegenüber der in
den Tabellen für das Schneiden angegebenen Nominal-Lichtbogenspannung vorgenommen werden.
Der wichtige Punkt bei der Steuerung während eines Schnittes ist der Abstand zwischen Brenner und
Werkstück. Die Lichtbogenspannung ist einfach eine indirekte Methode zur Steuerung dieser Höhe.
2.
IHS-Rückzug oder Lochstechhöhe einstellen
Den unteren linken Drehregler zur Einstellung der IHS-Rückzugshöhe verwenden. Wenn dieser Regler
eingestellt wird, wird die Anzeige vorübergehend durch eine Bezugsebene von 0 bis 10 außer Kraft
gesetzt. Diese stellt die gewünschte Lochstechhöhe dar. Die tatsächliche Höhe sollte in den Tabellen für
das Schneiden, die mit der Plasmaanlage mitgeliefert wurden, verfügbar sein. Diese Einstellung ist ein
ungefährer Wert, der davon abhängt, ob die Einheit die Platte mittels ohmschem Kontakt abtasten kann,
oder ob sie sich auf die Reserve-Drosselkraft-Abtastung verlassen muss.
Diese Einstellung ist zu überprüfen, indem ein IHS-Test vorgenommen wird und indem geprüft wird, ob
die Lochstechhöhe korrekt ist. Immer wenn der untere linke IHS-Test-Schalter gedrückt wird, wechselt
der Brenner zwischen der eingestellten IHS-Höhe und der Rückzugshöhe bei Schnittende. Test
fortsetzen und Feinabstimmung dieser Einstellung vornehmen, bis die gewünschte IHS-Höhe erreicht ist.
Wenn der DIP-Schalter (SW5) für die IHS-Geschwindigkeit auf die normale Niedergeschwindigkeits-
Einstellung eingestellt worden ist, sollte der IHS-Rückzugs-Regulierungsbereich zwischen 0,13 – 13 mm
liegen. Wenn der DIP-Schalter (SW5) für die Hochgeschwindigkeits-Einstellung eingestellt worden ist, sollte
der IHS-Rückzugs-Regulierungsbereich zwischen 2,5 – 25 mm liegen.
3.
Lochstechverzögerungszeit einstellen
Unteren rechten Drehregler zur Einstellung der Lochstechverzögerung verwenden. Wenn dieser
Regler justiert wird, ist die Anzeige vorübergehend durch eine Bezugsebene von 0 bis 4.0 als zweite
Verzögerungszeit außer Kraft gesetzt. Dies ist die Zeitverzögerung zwischen der Zündung des Brenners
und dem Beginn des Schneidvorschubs. Die Lochstechverzögerung ist die vom Brenner benötigte
Zeit, um zu Beginn die Platte zu durchschneiden. Diese Zeitverzögerung sollte in den Tabellen für das
Schneiden enthalten sein, die mit der Plasmaanlage zur Verfügung gestellt werden. Um eine höhere
Genauigkeit für die kurzen Verzögerungseinstellungen zu gewähren, ist dieser Drehregler in 2 Bereiche
aufgeteilt. Der erste Bereich umfasst die erste Hälfte der Reglerumdrehung und sorgt für eine lineare
Verzögerung von 0 bis 1 Sekunde. Die zweite Hälfte der Umdrehung umfast eine lineare Verzögerung
von 1 bis 4 Sekunden.